Applications
- Flotation
- Air knife
- Dewatering
- Combustion
- Fluidization
- Gas handling
- Carbon black
- Desalination
- Gas sampling
- Galvanization
- Steam handling
- Vacuum cleaning
- Sulphur recovery
- Pneumatic conveying
- Wastewater treatment...
Inert
Helium (He)
Argon (Ar)
Carbon dioxide (CO2)
Nitrogen (N2)
CO2 & Nitrogen mixture
Toxic
Ammonia (NH3)
Hydrogen chloride (Hcl)
Carbon dioxide (CO2)
Acid gases
Dry chlorine
Corrosive
Hydrogen chloride (Hcl)
Acid gases
Nitrogen & Alcohol
Vapor
Flue gas
Coke oven gas
Biogas
Flammable
Propane (C3 H8)
Natural gas
Alcohol vapor
Toluene (C6 H5 CH3)
Ethylene (C2H4)
Miscellaneous Hydrocarbon gases
Oxygen (O2) - Methane (CH4)
Monochlorobenzene
Sewage or waste gases - Biogas
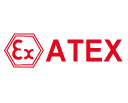
Áreas de risco de explosão requerem sopradores especiais. A Continental oferece sopradores ATEX para aterro sanitário e biogás.
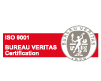
Bureau Veritas Certification ISO 9001: 2008 Desenvolvimento e fabricação de exaustores e sopradores centrífugos de múltiplos estágios.